Supply Chain Returns Management Solutions
Efficient returns management is crucial for maintaining customer satisfaction and recovering value from returned goods. Shyftbase's reverse logistics platform streamlines the entire returns process while maximizing recovery value.
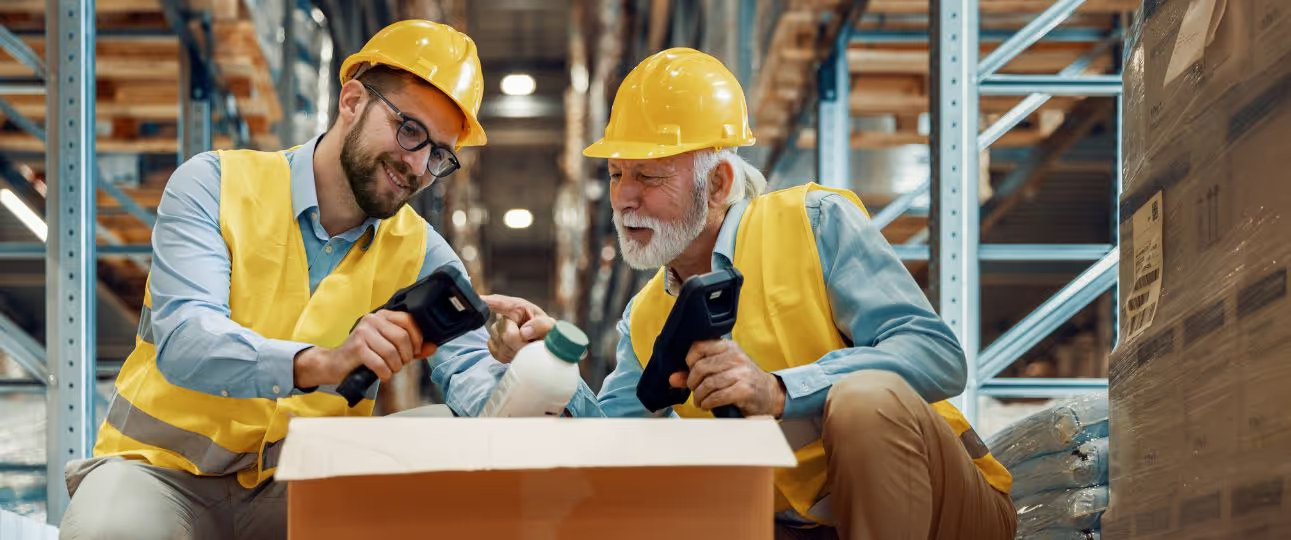
cutting edge solutions
How Shyftbase Simplifies Returns Operations
Shyftbase provides comprehensive control over reverse logistics while seamlessly connecting returns processing with forward logistics operations.
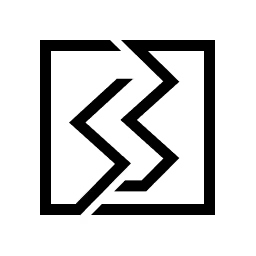
Automated Returns Processing
Streamlined returns authorization and processing workflows reduce handling time and improve efficiency.
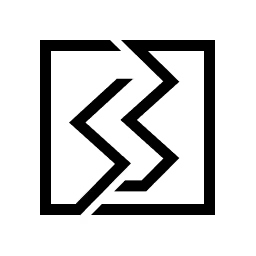
Smart Disposition Management
AI-powered disposition recommendations optimize value recovery from returned goods.
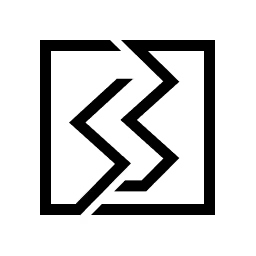
Integrated Customer Communications
Automated status updates and tracking improve the customer experience while reducing support requirements.
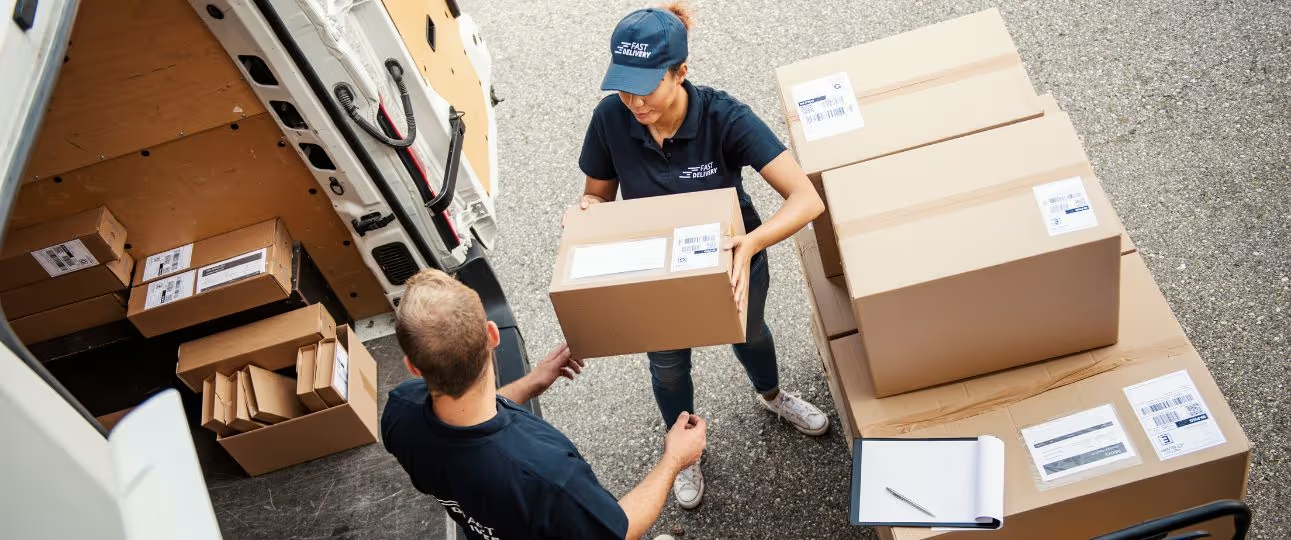
common roadblocks
Common Challenges in Supply Chain Returns
Organizations struggle to process returns efficiently while maintaining customer satisfaction and maximizing recovery value.
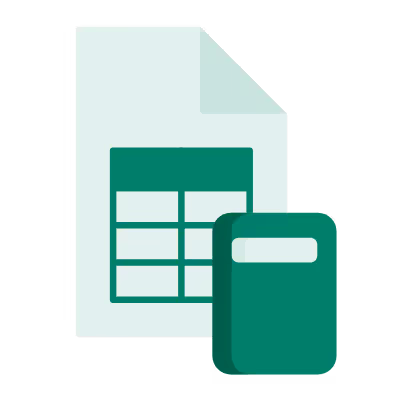
Challenges in Cost Control
Cost control is a critical aspect of supply chain management, as it directly impacts profitability. Companies must identify cost-saving opportunities, eliminate inefficiencies, negotiate favorable terms with suppliers, and optimize resource utilization to manage costs effectively. Implementing cost management tools and regularly reviewing financial performance can help maintain control over expenses and improve financial outcomes.
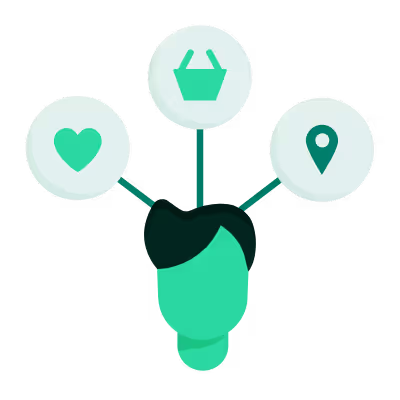
High Customer Satisfaction Expectations
Meeting customer expectations is a critical challenge in supply chain management, as it directly impacts customer satisfaction and loyalty. Customers increasingly demand fast, reliable, and transparent service. Companies must invest in technologies that enhance visibility, streamline operations, and improve communication to meet these expectations and maintain a competitive edge.
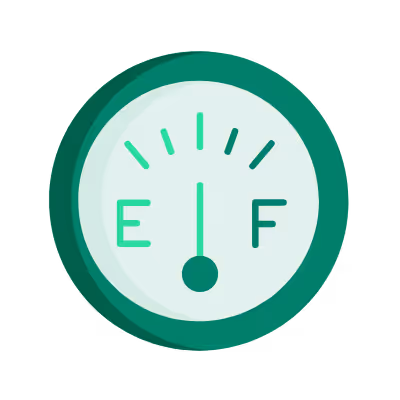
Rising Fuel Costs
Fuel costs are a significant expense in logistics operations, impacting overall transportation costs. Fluctuations in fuel prices can disrupt budgeting and financial planning. Companies must implement fuel-efficient practices, invest in alternative fuel vehicles, and optimize delivery routes to manage fuel costs effectively and reduce their environmental impact.
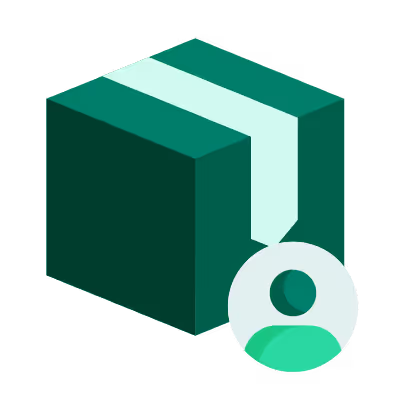
Inaccurate Inventory Management
Effective inventory accuracy and management is is crucial for maintaining optimal stock levels, reducing carrying costs, and ensuring timely order fulfillment. Implementing robust inventory management systems, conducting regular audits, and using real-time tracking technologies are key to both customer satisfaction and financial performance.
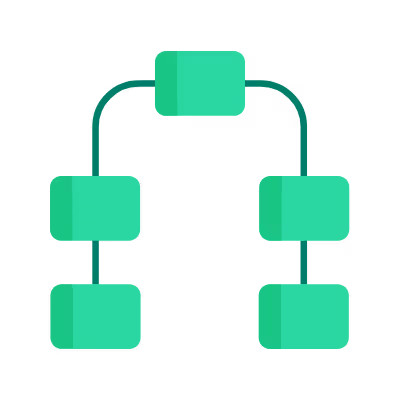
Low Processing Efficiency
Processing efficiency involves optimizing production and logistics processes to reduce costs and improve speed. This challenge requires the use of advanced technologies, such as automation and data analytics, to identify inefficiencies and implement improvements. By enhancing processing efficiency, companies can increase productivity, reduce lead times, and improve customer satisfaction.
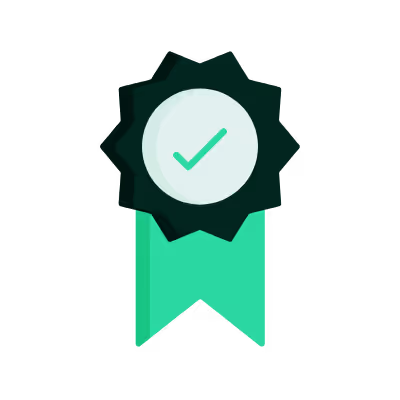
Inadequate Quality Control
Quality control is essential to ensure that products meet customer expectations and regulatory standards. Implementing robust quality management systems, conducting regular audits, maintaining strong supplier relationships, and fostering a culture of continuous improvement are key. By maintaining high-quality standards, companies can reduce returns, enhance customer satisfaction, and protect their brand reputation.
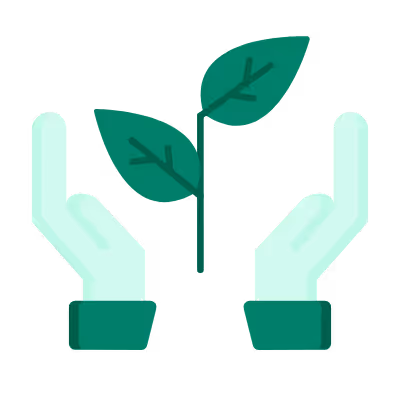
Meeting Sustainability Requirements and Reducing Environmental Impact
Sustainability requirements are increasingly important for companies aiming to reduce their environmental impact, comply with regulatory standards, and meet stakeholder expectations. Achieving these goals requires integrating sustainable practices such as reducing emissions, minimizing waste, and optimizing resource use into all aspects of the supply chain, from sourcing to production to distribution. Companies must collaborate with suppliers to ensure compliance with sustainability criteria, invest in eco-friendly green technologies, and transparently report their environmental performance to stakeholders.
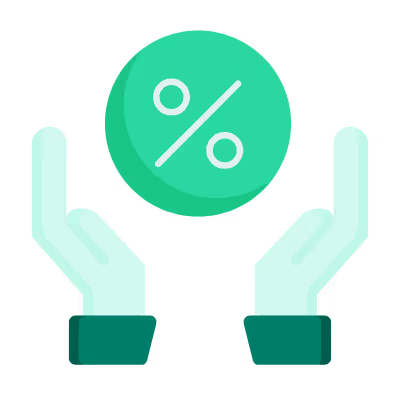
Challenges in Value Recovery
Value recovery involves maximizing the value of returned or excess products through processes such as refurbishment, recycling, or resale. This challenge requires efficient reverse logistics operations and collaboration with partners to recover value from products that would otherwise be wasted. Implementing value recovery strategies can enhance sustainability, reduce costs, and improve profitability.
Here's Where Shyftbase Shines
Shyftbase has been instrumental in reshaping our supply chain into a strategic asset. Before Shyftbase, our supply chain was a complex puzzle with many missing pieces. Their platform provided the capabilities we needed to manage every point of the order lifecycle effectively. This has led to significant reductions in manual errors, cost savings across the board, and, most importantly, a surge in our team's productivity.
Cameron Wheler
Implementation Manager
Metro Supply Chain
Visibility with our 3PL providers was the Achilles' heel of our logistics operations before Shyftbase. Implementing their platform, we achieved high degrees of transparency and efficiency, reducing our logistics costs by significantly and eliminating redundant steps in our order lifecycle. Shyftbase has been pivotal in streamlining our operations and boosting our bottom line.
Jeremy McQueen
Director of Operations
Custom Delivery Solutions
Our partnership with Shyftbase made it possible for us to offer same-day delivery. Previously, the concept of same-day delivery meant a ton of complications. However, Shyftbase’s solution enabled us to slash delivery times, directly leading to tangible improvements in customer satisfaction scores. It’s not just a software; it’s our competitive edge in logistics.
Moez Premji
Director of Operations
Custom Delivery Solutions
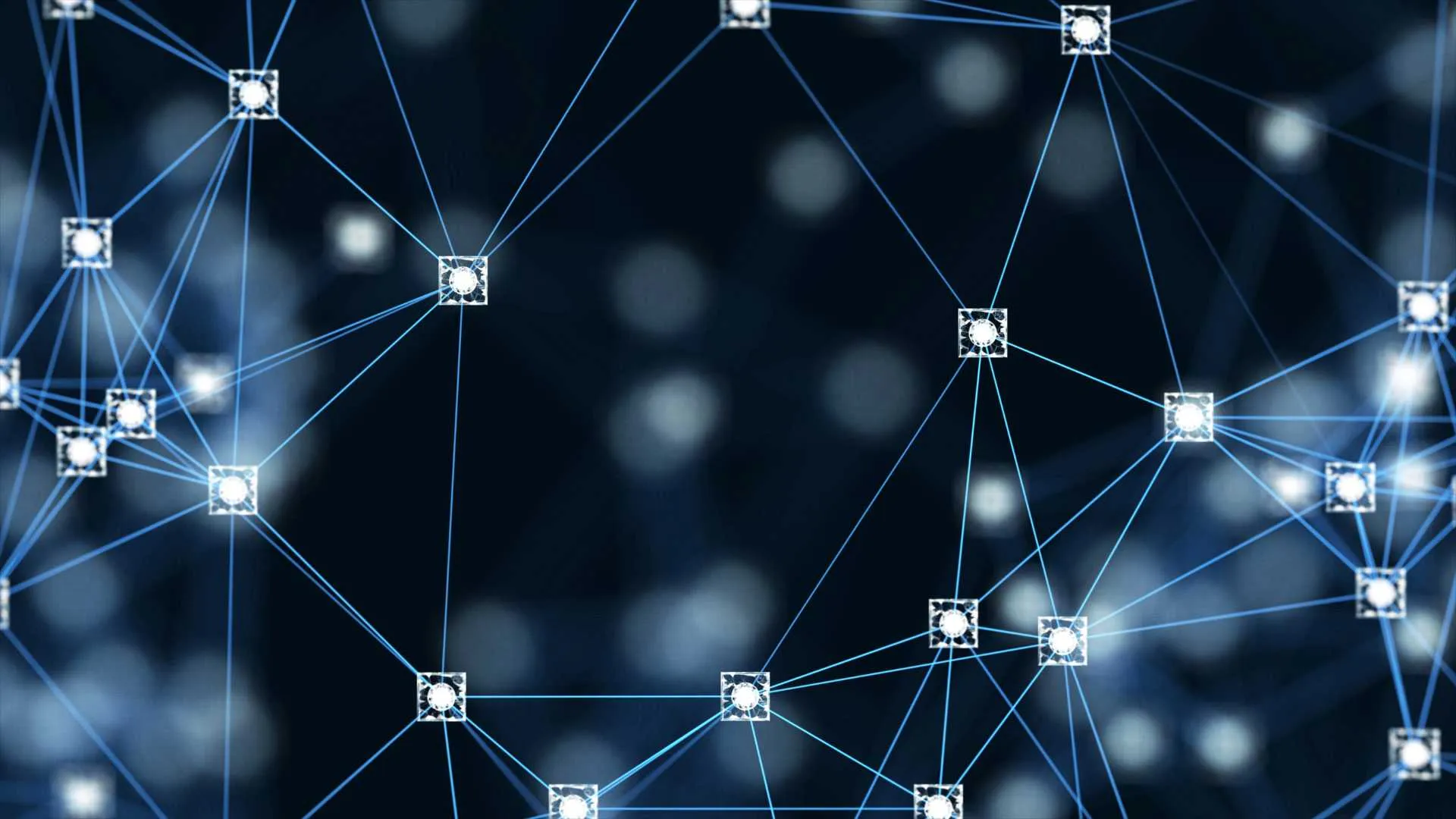
Overcome anything
Maximize Returns Management ROI
See how Shyftbase can help you transform returns management from a cost center into a value driver. Schedule a demo to explore our reverse logistics solutions.
FAQs
If you have a question which isn't listed here, feel free to connect with our team.
How does Shyftbase improve route planning and optimization?
Shyftbase routing engine is capable of routing by zone, limiting to a portion of the volume, and integrated delivery and install routing. Shyftbase includes communication tools that facilitate seamless interaction with carriers and drivers, improving efficiency accross your team.
What is Shyftbase Transportation Management Software (TMS)?
Shyftbase is a powerful supply chain solution that allows customized control over every aspect of the full order lifecycle - so you can increase profit and elevate your customer experience.
Can pickup scheduling be automated?
Yes, Shyftbase automates pickup scheduling based on customer requests, service availability, and route optimization. The system coordinates timing with existing delivery routes to maximize efficiency and minimize costs.
How does Shyftbase manage return pickups?
Shyftbase coordinates return pickups by linking them to original deliveries, automating scheduling, and organizing efficient routes. The system maintains complete visibility and tracking throughout the reverse logistics process.